HOW ELECTROPLATING HAVE BEEN DONE
Electroplating is defined as an electrodeposition process, which uses an electrode to pass current to make metal adhere to the surface of an object. Its purpose is to change the characteristics or size of the surface of the object.
The purpose of electroplating is to deposit a metal coating on the substrate to change the surface properties or size of the substrate.
For example, to give metal luster and beauty, to prevent rust, to prevent abrasion, to improve electrical conductivity, lubricity, strength, heat resistance, weather resistance, heat treatment to prevent carburization, nitriding, size error or abrasion repair of parts.
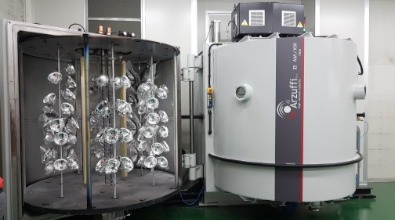
Vacuum plating uses a strong current to heat the plating source (tungsten wire), and then melts the aluminum sheet or wire hanging on the tungsten wire. The aluminum thus evaporates, scatters to all sides, and adheres to the plated article. The molten aluminum is aluminum atoms, which exist in an amorphous or liquid state and adhere to the workpiece to be plated. After cooling and crystallization, it becomes an aluminum film.
From the degree of vacuum to the scattering direction of the evaporated aluminum, the temperature of the tungsten wire, the distance between the tungsten wire and the part to be plated, etc., depending on the coating conditions, the performance of the coating also changes in addition to changes.
For example, when the vacuum degree and the temperature of the tungsten wire are high, the kinetic energy of evaporating aluminum will also increase. The surface of the coated part will be pure aluminum (with no residual gas), and the density will be very high, so the coating performance will be improved ( Including adhesion, etc.).